Introduction
Diesel generators play a crucial role in providing backup power during blackouts or in remote locations where grid power is unavailable. These generators are known for their reliability and ability to operate for extended periods, making them essential for critical applications such as hospitals, data centers, and manufacturing facilities. However, like any other machinery, diesel generators are susceptible to faults that can compromise their performance and reliability. Fault detection in diesel generators is essential to ensure continuous operation and prevent costly downtime. In this article, we will explore the importance of fault detection in diesel generators and discuss various methods and technologies used for detecting faults.
Importance of Fault Detection in Diesel Generators
The reliable operation of diesel generators is crucial for maintaining continuous power supply in various applications. https://www.lkpowerplant.com/product/quick-delivery-emergency-standby-power-400kw-silent-type-diesel-generator-set-for-peru/ or malfunction in a diesel generator can lead to disruptions in power supply, resulting in financial losses, damage to equipment, and potential safety hazards. Fault detection in diesel generators plays a vital role in preventing these issues by identifying potential problems before they escalate into major failures.
Early detection of faults in a diesel generator allows for timely maintenance and repairs, minimizing downtime and reducing the risk of costly repairs. By monitoring key parameters and performance indicators, operators can identify abnormal patterns or deviations that may indicate an underlying issue. Fault detection systems provide real-time alerts and notifications, allowing operators to take corrective actions promptly and prevent potential failures.
Methods and Technologies for Fault Detection in Diesel Generators
There are various methods and technologies employed for fault detection in diesel generators, ranging from simple visual inspections to advanced monitoring systems. Some of the common methods used for fault detection in diesel generators include:
1. Visual Inspection: Visual inspection of a diesel generator involves examining the exterior components, connections, and overall condition of the generator for any signs of wear, corrosion, or damage. Visual inspection can help identify obvious issues such as loose connections, leaks, or physical damage that may indicate a potential fault.
2. Acoustic Monitoring: Acoustic monitoring involves using sensors to detect abnormal sounds or vibrations in the diesel generator. Unusual noises or vibrations can be early indicators of mechanical issues such as bearing wear, misalignment, or imbalance, which can lead to failure if not addressed promptly.
3. Oil Analysis: Regular oil analysis is a common method for detecting internal problems in a diesel generator. By analyzing the oil for contaminants, metal particles, or abnormal wear patterns, operators can identify issues such as engine wear, fuel contamination, or overheating that may affect the generator's performance.
4. Vibration Analysis: Vibration analysis is used to monitor the vibration levels of critical components in a diesel generator, such as the engine, alternator, and bearings. Changes in vibration patterns or amplitude can indicate misalignment, imbalance, or wear, allowing operators to diagnose and address potential faults.
5. Thermal Imaging: Thermal imaging technology is used to detect overheating or hotspots in a diesel generator's components. By capturing infrared images of the generator while in operation, operators can identify areas of excessive heat that may indicate electrical faults, insulation breakdown, or cooling system issues.
6. Remote Monitoring Systems: Remote monitoring systems utilize sensors, data loggers, and communication technology to continuously monitor key parameters of a diesel generator, such as temperature, pressure, fuel level, and performance metrics. These systems provide real-time data and alerts to operators, enabling proactive maintenance and fault detection.
7. Condition-Based Maintenance: Condition-based maintenance strategies use a combination of data analysis, predictive modeling, and machine learning algorithms to predict and prevent potential faults in diesel generators. By analyzing historical data and performance trends, condition-based maintenance systems can identify patterns that may lead to failures and recommend preventive actions.
Benefits of Fault Detection in Diesel Generators
Implementing a robust fault detection system in diesel generators offers several benefits, including:
1. Improved Reliability: By detecting faults early and implementing timely maintenance measures, the reliability of diesel generators can be significantly enhanced. Preventing unexpected failures and downtime ensures continuous power supply and operational continuity in critical applications.
2. Cost Savings: Proactive fault detection and maintenance help reduce repair costs, minimize downtime, and extend the lifespan of diesel generators. By addressing issues before they escalate, operators can avoid costly repairs and replacements, resulting in cost savings in the long run.
3. Enhanced Safety: Fault detection in diesel generators contributes to enhancing safety by preventing potential hazards such as electrical fires, overheating, or mechanical failures. Timely identification of faults allows for corrective actions to be taken to mitigate safety risks.
4. Optimal Performance: Maintaining a diesel generator in optimal condition through fault detection and preventive maintenance ensures consistent performance and efficiency. By addressing faults promptly, operators can maximize the generator's output and minimize energy wastage.
Conclusion
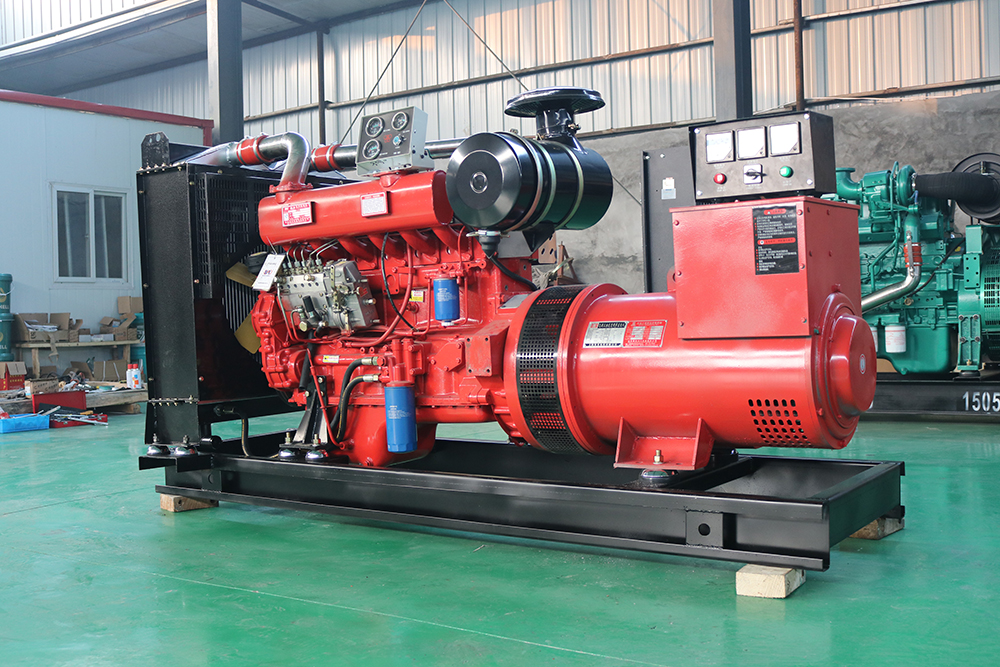
Fault detection in diesel generators is essential for ensuring the reliable operation of backup power systems in critical applications. By employing various methods and technologies for fault detection, operators can proactively monitor the condition of diesel generators, identify potential issues, and take timely corrective actions to prevent failures. Implementing a comprehensive fault detection system offers numerous benefits, including improved reliability, cost savings, enhanced safety, and optimal performance. As the demand for reliable power supply continues to grow, the importance of fault detection in diesel generators cannot be overstated. By prioritizing fault detection and maintenance practices, operators can safeguard their diesel generators against unexpected failures and ensure uninterrupted power supply in essential facilities.